Projects are conceived by a results oriented team effort, to produce a product or machine to meet and exceed the customer requirements. To produce this effort, we proceed with an in depth study verifying environment, ergonomic requirements, production rate, system integration, alternative methods, and other contributing factors necessary to produce a turnkey project
Following the concept formation, design begins using solid modeling to produce visual representations of key areas, followed with client approval. If necessary, a rendered animation can be created.
Final documentation package can include a complete set of drawings, layout, assembly/sub-assembly drawings, detail drawings, electrical, pneumatic and hydraulic schematics as well as purchased items part numbers with vendor information.
We can also supply a recommended spare parts list with preventive maintenance documentation, and a detailed operations manual. Validation packages for the pharmaceutical industry are also available.
Final FAT (Factory Acceptance Test) and prove out of the project is accomplished at the Carolina Mechanical facility with our company manpower or the client personnel.
Project Installation is always performed by qualified Carolina Mechanical personnel with on-site supervision by the Project Leader. The project leader will be responsible for training along with the Controls Engineer.
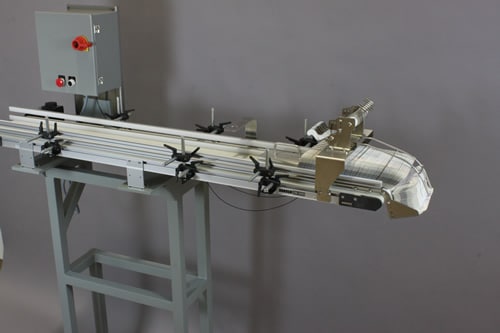
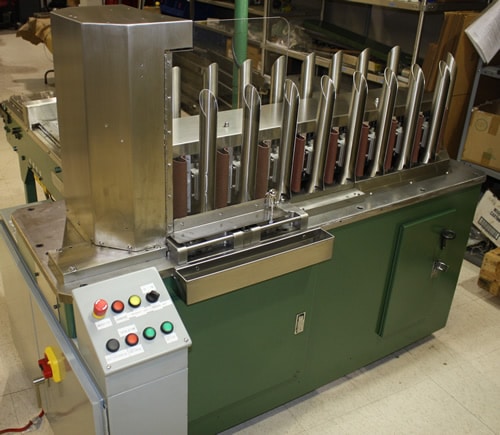
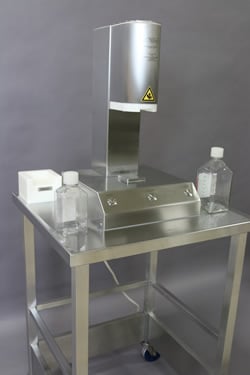
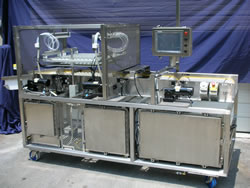
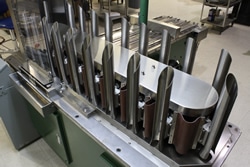
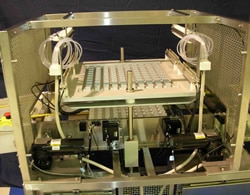
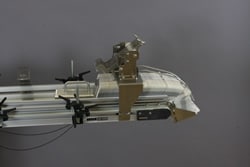